I. Background Description In the process of power plant coal conveying, the coal is ground into a fine powder after grinding by a coal mill. The dust is large and there is a strong adsorption property that will be adsorbed on the surface of the level gauge. The traditional material level Measurement methods such as radar, guided wave radar, and 3D imaging cannot accurately obtain level information. The 700T silo often uses only 2/3 of the space, and there is also the risk of shortages and explosions. At present, the entire country is also actively promoting the intelligent management of coal-fired power generation, and measuring by points and bins. In view of this, the brand-new patch type technology of US KM Corporation is an indirect measurement method. This method does not directly detect the height of the material level, but responds to the status of the material by detecting the deformation of the silo legs. Do not consider the dust concentration, hanging material, stacking angle, landslide, etc. in the warehouse.
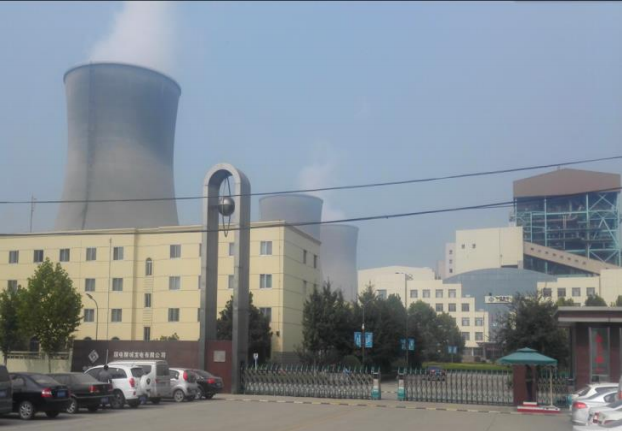
Figure 1 Project Reality
Second, the technical analysis of the implementation of the project's silo is a typical steel silo, capacity 700T or so. Because the supporting legs are made of carbon steel, the supporting legs are elastically deformed when loading and unloading materials. These deformation variables are proportional to the weight of the load. As long as these tiny deformations are detected, the weight of the material in the silo can be known.
Special tools Kistler-Morse® brand Microcell patch sensors are tightly fastened to the bin's legs by bolts. Deformation of the legs also drives the patch-type transducers to deform together, via the ultra-high-sensitivity strain gauges inside the sensor. "The deformation of the leg, the deformation of the variable into electrical signals, the final calculation of the silo weight value.
This program uses 8 pieces of Microcell-type patch-type level meter, a sensor attached to the legs of each silo, using the junction box to summarize the data into the KM-specific controller, the controller will amplify the weak signal output by the sensor Processing as a digital signal, and output a 4 ~ 20mA signal to the host computer system.
Third, the accuracy analysis After field measurement, the size of the I-beam "300 × 335 (web) × 30 (thickness)" to roughly calculate the pressure. The cross-sectional area of the eight support legs is (300+300+335)*30*8=224400. The pressure at 700T is: 700,000/224400=3.12kg/mm2
According to the accuracy calculation table, the accuracy at a pressure of 3.12 kg/mm2 is approximately +/-1.5% (+/-10.5T). In this case it is very suitable for the work of patch systems.
Note: This accuracy depends on the form and size specifications of the silo legs. Different bins will have different accuracy performance. Please provide accurate technical parameters for the silo legs to facilitate a more accurate understanding of the accuracy of the product
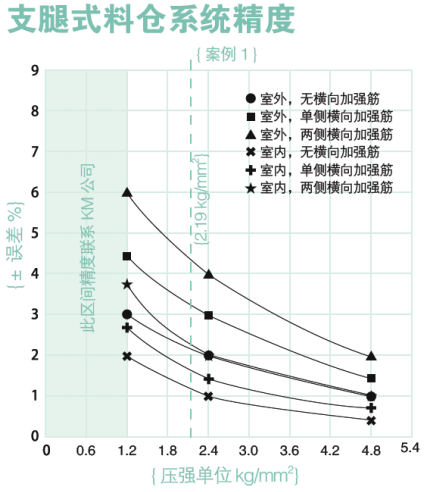
Figure 5: SMD weight level gauge accuracy table
Fourth, the project implementation SMD sensor installation is very convenient, only need to open three 3.4mm holes, without destroying the support structure. The fastest time to install a sensor is only 15 minutes. There is no need to stop the production during the installation, and it is not necessary to empty the silo.
Microcell patch sensor installation process is relatively simple, do not need to climb operations, do not need large equipment, only 2 individuals, and some readily available tools to complete the installation task.
V. Use effect From the customer's office, the raw coal bunker consumes about 50 tons of coal per hour, and the consumption is relatively even. Then the change in the weight value from the patch type reading should also be uniform. Since the SMD system has been connected to the customer's DCS system, we continue to observe the data from the DCS system. This data should also be evenly changed. It can be seen from Figure 9 that when the system loads and uses materials, the weight value changes very evenly and there is no jumping or missing data.
Looking closely at this graph (Figure 10), we took a portion of the data to observe: From 2:14 am to 4:14 pm, the weight value of the patch display was reduced by 100T from 2 hours to 4:14 am. The consumption of 50 T coal per hour is very consistent. Visible patch weight level meter is very suitable for the application of raw coal bunker
VI. Conclusion For thermal power plants, the Kistler-Morse® SMT metering system of the United States has high accuracy, easy installation, and convenient maintenance. It does not affect the normal in- and out-feed at the site during the installation process. The construction cost is extremely low. Can be easily applied to new projects and equipment reconstruction. As a level measurement, especially solid material level measurement in harsh environments is a very good choice!